Новые технологии переработки бытовых и промышленных отходов
Опубликовано Редактор 25-11-2003 (5171 прочтений)Например, по данным ГОХРАН в России скопилось около 500 тыс. тонн военного электронного скрапа, содержащего 300 тонн золота, причем этот объем ежегодно пополняется на 12 %. Военный электронный скрап содержит от 0,3 до 3 кг золота на 1 тонну, а гражданский - от 70 до 150 г на тонну скрапа, что, как минимум в, 20 раз больше, чем в руде. Причем золото извлекается со значительно меньшими затратами, чем из руды и при этом попутно получают другие драгоценные и цветные металлы.
Большинство отходов относится к возобновляемым ресурсам, что неизбежно приводит к снижению эксплуатации природных источников. Даже пищевые отходы можно превратить в плодородную землю, более богатую полезными для растений компонентами, чем природная земля.
В богатых странах многие бытовые и промышленные отходы, которые выгодно могут быть регенерированы, направляют в отвалы и засыпают слоем почвы. В большинстве стран бытовые отходы сжигают полностью, иногда используя тепловую энергию и при этом, например, в ряде европейских стран, за такую работу получают бюджетные дотации в размере 80—100 USD за сжигание 1 т мусора. Токсичные диоксиновые выбросы от процесса сжигания при низких температурах (до 1100 °С) полностью не могут быть нейтрализованы и поэтому представляют вред для населения, вызывая разного рода мутации. Ранее бытовавшее мнение о целесообразности сжигания мусора при более высоких температурах (более 1150 °С), при которых диоксины разрушаются, в настоящее время не получает подтверждения, т, к. образующиеся при этом более короткие молекулы иногда проявляют еще большую химическую активность и токсичность.
Причиной отсутствия должного внимания к переработке разнообразных отходов является отсутствие в этой области эффективного технологического оснащения. Ведь различные компоненты отходов требуют своего способа дробления, классификации и сепарации. Поэтому попытки комплектации перерабатывающих заводов специальным оборудованием не универсального действия приводили к крайне высоким капитальным затратам и обуславливали их нерентабельность.
Любые промышленные или бытовые отходы должны быть измельчены, расклассифицированы и отсепарированы. Только в этом случае выделенные компоненты могут быть реализованы и принесут прибыль. Однако традиционное оборудование для этих процессов безнадежно устарело и требует новых идей для его совершенствования.
Самыми распространенными процессами как для переработки сырья, так и отходов являются дробление и измельчение. Вообще в современном индустриальном производстве эти процессы поглощают около 20 % электроэнергии вырабатываемой человечеством.
Такие большие затраты электроэнергии объясняются тем, что в современных дробильно-измельчительных машинах применяются процессы разрушения, освоенные еще первобытным человеком: сжатие, удар, истирание, резание. При таком воздействии материал разрушается беспорядочно, почти без использования микротрещин и других дефектов его структуры. Кроме бесполезных затрат энергии, существующие дробильно-измельчительные процессы приводят к безвозвратным потерям полезных компонентов или к существенному ухудшению свойств производимых из них продуктов из-за неполного измельчения или, наоборот, переизмельчения, скатывания или повреждения частиц.
При обогащении руд по этим причинам теряется до 15-30 % металла. Этот недостаток относится и к извлечению драгоценных металлов. Полезные компоненты уходят в хвосты.
При переработке древесины методом резания в дисковых мельницах существенно укорачиваются и повреждаются волокна, что не позволяет сделать бумагу более прочной и тонкой, а большая часть энергии затрачивается бесполезно, поэтому и здесь по этой причине образуется много отходов.
При производстве пищевых продуктов и кормов оболочки большинства клеток не раскрываются, поэтому усвояемость полезных компонентов клеток не превышает 70 %.
При производстве дорожного щебня уходит в отсевы почти 45 % гранита — это тоже не только потеря энергии, но и потеря ресурсов.
При получении цемента из клинкера снижается площадь поверхности его частиц, а сверхтонкие частицы за счет электростатики объединяются друг с другом в агрегаты. Это приводит к повышению расхода цемента на 10 — 20 %, а прочность бетона снижается из-за шариков "спящего" цемента.
Переработка промышленных отходов существенно усложняется в одних случаях из-за неселективности разрушения, в других - из-за необходимости использования термических методов, химических реагентов и воды.
На основе фундаментальных исследований в области физики твердого тела и теории колебаний разработаны новые способы и оборудование, позволяющее почти полностью исключить перечисленные недостатки и снизить затраты энергии: в два раза при переработке минералов, в пять раз при переработке древесины и других растительных материалов и в двадцать раз при переработке металлов. При этом объем отходов снижается на 20 %.
Сущность процесса заключается в принудительном самоизмельчении материала внутри собственного слоя под воздействием виброимпульсного сжатия с одновременным сдвигом при дозировании силы воздействия на слой материала до величины предела прочности дефектных поверхностей его структуры. Разрушение осуществляется телами с гладкими рабочими по верхностями: плитами, конусами, цилиндрами.
Машина, реализующая такой процесс, универсальна и может по желанию владельца производить щебень для дорог, цемент или до заданного гранулометрического состава измельчить руду, мел, древесину, траву и разнообразные отходы.
Процесс может осуществляться всухую или с подачей воды. Если требуется получать очень тонкие частицы, то измельчение осуществляется в замкнутом цикле с гидро- и пневмосепараторами. Степень измельчения плавно регулируется от 4 до 100. на перенастройку машины требуется не более 15 минут.
Созданные в АО "Механобр - Техника" новые дробильно-измельчительные машины могут объединяться с грохотами, конвейерами, элеваторами и сепараторами (магнитными, электрическими, гравитационными и пневматическими) в компактные фабрики различного назначения, в частности для переработки отходов. Такие фабрики имеют в два - три раза меньше энергопотребление и занимаемые площади, не требуют фундаментов и дозаторов, расход материала и мелющих тел на них в 20 раз ниже, чем на традиционных современных фабриках.
Фабрики могут иметь микро- и макроразмеры и производительность до многих миллионов тонн в год и способны перерабатывать материалы любой прочности: бумагу (в том числе с полиэтиленовым покрытием), корма, пищевые продукты, регенерировать литейные пески, шлаки, абразивные круги, отходы керамических изделий, автопокрышки, железобетон, электронику, пластмассы и бытовые отходы.
С помощью оборудования АО "Механобр - Техника" могут перерабатываться отходы различных отраслей промышленности.
Промышленность строительных материалов
Железобетонные отходы в виде стеновых панелей, блоков и свай могут перерабатываться в виброщеко-вых дробилках (рис. 1) за один проход до крупности 50 мм и мельче при одновременном отделении арматуры. Доизмельчение таких кусков в конусных вибрационных дробилках до цементной крупности позволяет активизировать "спящий" цемент и получать порошок, сокращающий расход цемента на 30 %.
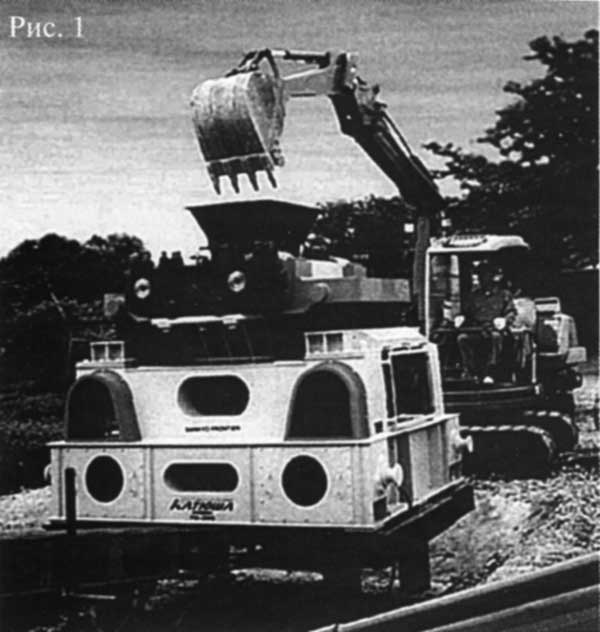
Вибрационные дробилки уже в течение 20 лет успешно используются в Японии и других странах для производства щебня и искусственного песка из отвалов горных пород. Частицы щебня и песка имеют форму, близкую к кубической (до 95 % кубовидности), при минимальной трещиноватости и почти без отходов на переизмельчение.
Регенерация лежалого (застывающего) цемента с помощью вибродробилок позволяет получать цемент марки 300.
С помощью виброизмельчительных машин удалось радикально упростить производство строительной керамики из отходов. Отпала необходимость использования шаровых мельниц, а прочность плитки повысилась на 30 %, водопоглащение снизилось на 20 %, брак практически отсутствует.
Металлургическая промышленность
Способность вибрационных дробилок перерабатывать весьма прочные материалы позволяет их использовать для переработки металлургических шлаков, содержащих до 50 % металлов. При этом извлекается до 95 % металлов. Учитывая, что в России скопились десятки миллионов тонн шлаков черных и цветных металлов их переработка выгоднее, чем руды.
Регенерация литейных песков и огнеупоров также резко упрощается благодаря отказу от термических и водоочистных процессов. Связка удаляется с поверхности кварцевого песка путем виброоттирки в конусной вибродробилке и отделяется воздушным сепаратором, а частички металла собираются электростатическим сепаратором.
Изделия из регенерата обладают повышенным сроком службы благодаря устранению термических трещин в процессе виброизмельчения отходов. Возврат регенерата достигает 88 %. Остальные 12 % составляет отделенная связка, используемая в дальнейшем вместо цемента или коагулянта.
На рис. 2 показана схема регенерации литейных (формовочных) песков.
Металлообрабатывающая промышленность
Регенерация абразивного инструмента (электрокорунды, эльбор, алмазы) существенно упрощаются благодаря применению вибродробилок. При этом достигаются следующие эффекты:
- снижение переизмельчения на 18 - 20 %;
- получение изометрического зерна с минимальной трещиноватостью;
- устранение мокрого процесса и стержневых мельниц;
- снижение потребных площадей и оборудования, по крайней мере, в 3 раза;
- повышение стойкости изделий на 30 - 40 %.
В настоящее время единственными машинами, способными измельчать необожженный отработанный твердосплавный инструмент, являются конусные вибродробилки. Схема с их использованием показана на рис. 3.
В них удается получать порошок мельче 40 мкм. Затем он доизмельчается в аттриторах до крупности мельче 3 мкм. Такой порошок может быть вновь использован для производства инструмента. Может быть получена и твердосплавная крошка, используемая для производства специального инструмента, твердосплавных наплавочных электродов и наполнителей быстроизнашивающихся частей, например, зубьев экскаватора. Необходимая площадь для такой установки составляет не более 25 м2 вместо 3000 м2, используемых для традиционных термохимических процессов. При этом затраты энергии снижаются в 500 раз.
В настоящее время стружка после металлообработки переплавляется и при этом теряется ее марочность, а потери металлов достигают 20 %.
Виброоборудование позволяет отсортировать, отмыть и измельчить стружку до порошка, из которого методом порошковой металлургии изготавливаются высококачественные изделия. Тем самым заменяются сложнейшие процессы плавки, распыления, экструзии, металлообработки.
Резцы, полученные из измельченной стружки быстрорежущей стали, не уступают таковым, изготовленным методом сложной традиционной технологии.
Производство сварочных электродов с порошковой обмазкой существенно упрощается при использовании вибрационных измельчителей и классификаторов. Качество электродов при этом значительно повышается.
Переработка отходов электроники и электротехнического кабеля
По данным Японии и США, в 2000 году объем отходов электроники возрос в 4 раза в сравнении и 1994 г. К этим отходам относятся военная электроника, телевизоры, компьютеры, телефоны, радио, игровые автоматы, печи СВЧ и т.п. В европейских странах и США существующие установки, основанные на ручной разделке скрапа с использованием нескольких ножевых дробилок, электродинамических сепараторов и пирометаллургии. Линии отличаются большой металле- и энергоемкостью и уже не успевают перерабатывать большие объемы отходов, поэтому часть скрапа захоранивается.
Созданные в АО "Механобр - Технике" установки содержат одну ножевую дробилку, молотковую дробилку, а вместо электродинамических сепараторов -один электростатический. При производительности 500 кг/ч и установочной мощности 100 кВт установка занимает площадь 80 м и не требует фундамента. Установка принимает электронные блоки размером до 500 мм и куски кабеля длиной до 1500 мм.
Получаемый электронный металлический концентрат может быть разделен на отдельные драгоценные и цветные металлы с помощью упрощенной технологии пирогидрометаллургии.
При переработке военного электронного скрапа установка стоимостью $ 150 000 окупает себя за 25 дней после пуска, а при переработке кабеля - за 60 дней.
Схема установки показана на рис. 4.
Продолжением установки является отработанный пирогидрометаллургический процесс, который позволяет получать драгоценные металлы 99 %-ной чистоты и цветные металлы.
Переработка макулатуры и отходов древесины
Бумажная промышленность занимает четвертое место в мире по потреблению электроэнергии из-за использования режущих ножевых дисковых мельниц для измельчения древесной щепы. Процесс резания, разрыва и "жевания" щепы в таких мельницах крайне не рационален, т. к. при этом сокращается длина волокна и мало эффективно химическое ослабление межволоконных связей. При этом на вредное действие бессмысленно затрачивается энергия. Такой процесс приводит к ухудшению качества и прочности бумаги и к увеличению ее толщины. Кроме того, химическая подготовка щепы вызывает определенный объем брака (непровар), который традиционными методами переработать невозможно и он идет в отходы.
Новый виброизмельчительный процесс основан на импульсном сжатии слоя щепы с одновременным сдвигом. Процесс осуществляется между наружным и внутренним вибровзаимодействующими конусами.
Сила взаимодействия конусов настраивается так, чтобы существенно не превышать прочности межволоконных связей. Таким образом, повреждение волокон исключается. Затраты энергии снижаются по крайней мере в 5 раз, прочность бумаги на разрыв увеличивается в 2 раза, а на изгиб - в 20 раз. Износ гладких мелющих тел в несколько раз ниже, чем в ножевых дисковых мельницах, и не влияет на качество продукта. Таким образом, отходы щепы эффективно перерабатываются.
Промышленные испытания виброконусной дробилки (производительность - 50 т/сутки по сухой древесине) при измельчении отходов лиственной щепы в бумажную массу на Балахнинском ЦБК прошли успешно и подтвердили упомянутые показатели.
Такая же дробилка-мельница успешно перерабатывает в бумажную массу макулатуру, пакеты "Тетра -Пак" и бумагу с латексным и полиэтиленовым покрытием и изъятые из обращения деньги, что особенно актуально как для России, так и для Европы и США. Однако перед вибродробилкой должна быть установлена высокоскоростная молотковая дробилка с пластинчатыми билами. Такая дробилка обеспечивает получение из макулатуры бумажной эковаты как теплоизолятора При строительстве. Если нужно получать бумажную пульпу, то продукт этой машины направляют с водой в вибродробилку.
Смесь бумаги с пластиками перерабатывается в бумажно-пластмассовую массу, из которой могут производиться самые разнообразные изделия.
Отходы древесины могут перерабатываться с помощью вибродробилок-мельниц в корма с содержанием моносахаридов до 23 % при усвояемости 48 - 50 %. В отличие от традиционных новый процесс не требует автоклавов, высоких давлений и температур и не приводит к образованию вредных компонентов типа фурфурола, которые необходимо удалять из продукта. Процесс легко реализуется в фермерском хозяйстве.
Переработка автопокрышек
Автопокрышки с металлическим кордом перерабатываются без применения жидкого азота. Используются ножевая дробилка, молотковые дробилки для получения очищенной от металлического и текстильного корда резиновой крошки мельче 2 мм. Эта крошка перемешивается на вальцах со специальным модификатором, разрушающим сульфидные межмолекулярные связи в резине. В результате получается сырая резина, которая по качеству составляет 70 % от исходного. Добавление еще 2 - 5 % дешевых дополнительных
компонентов позволяет получать новую резину с физико-механическими свойствами до 90 % от первоначальной. Производительность установки - 2,5 т/ч. Расход модификатора - 4 % при его стоимости $ 3 за 1 кг. Себестоимость сырой резины $ 260 за 1 т, а рыночная стоимость $ 800 за 1 т. Эта российская технология уже 3 года используется на заводе в г. Сланцы Ленинградской области.
Переработка отходов стекла
В мировой практике ежегодно используется почти миллиард тонн химических удобрений, более половины из которых выветриваются, уходят с дождями в грунтовые воды, загрязняя окружающую среду. Капсулирование удобрений в полимерную пленку приносит лишь незначительный эффект.
Создание комплексных удобрений из растворимого стекла с использованием отходов стекла позволяет радикально улучшить сложившуюся ситуацию. Удобрения, внесенные в почву в том же количестве, что и традиционные, работают не один год, как традиционные, а 3 - 5 лет в зависимости от требования заказчиков. Удобрения не растворяются вовсе при отсутствии вегетации растений, т. е. при температуре ниже 8 °С. Удобрения содержат все необходимые компоненты для развития растений, причем их состав может регулироваться в зависимости от состава почвы и вида выращиваемой культуры. Производство удобрений осуществляется в обычной стекловарочной печи с последующим гранулированием или дроблением до 2 - 5 мм. Использование удобрений повышает урожайность на
30 - 40 %. Стоимость 1 кг удобрений не превышает $ 1 при производстве более 20000 т/год или $ 0,8 при производстве более 100 000 т/год.
Переработка отходов пластмасс Доля различных пластмасс в бытовых отходах составляет от 8 до 16 %, а стоимость их отдельных марок в гранулированном состоянии находится в пределах от 600 до 1000 USD за 1 т. Потому ручная сортировка пластмасс с последующей сепарацией и гранулированием является весьма прибыльным процессом.
Рабочие сортировочного конвейера сбрасывают в отдельные емкости полиэтиленовую пленку, пластмассовые бутылки (ПЭТФ) и другие пластики.
В соответствии с технологической схемой (рис. 5) пластмассы отдельно по сортам поступают на дробление с отделением бумаги, затем на мокрое дробление для отмывки пластика, далее на центрифуге и на вертикальном элеваторе пластмассы высушивают и частицы мельче 6 мм направляют на электростатический сепаратор, где они разделяются по маркам и в ряде случаев по цвету. Далее идет процесс агломерации пленки или гранулирования ПЭТФ и других пластиков. Гранулы уже являются готовым сырьем для производства изделий.
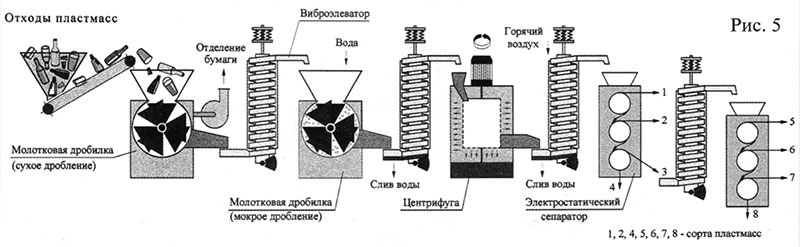
Если разборщики сортировочного конвейера более тщательно сортируют пластики, вплоть до отвинчивания пробок с бутылок, то дальнейшая переработка не требует электростатической сепарации.
Переработка бытовых отходов
Быстрый рост населения планеты требует повышения выработки энергии, стройматериалов, пищевых продуктов, бытовых товаров, пластмасс и бумаги. Все это в свою очередь ведет к резкому росту объемов отходов, которые потребуется не уничтожать, а превращать в полезный продукт. В большинстве стран бытовые отходы сжигаются или их используют для производства горючего газа, однако, в передовых странах наблюдается тенденция к частичному использованию некоторых компонентов бытовых отходов для их переработки и возврата в промышленность.
В России каждый человек выбрасывает в среднем 2 кг мусора в день, в США - 8 кг, а в Японии - 12 кг. Сейчас в Санкт - Петербурге в год накапливается около 1 млн. т мусора, а в Москве - 5 млн. т. Если в Москве мусор сжигают, то в Санкт-Петербурге частично используют для возврата металл и пластмассу, а остальное переводят в компост.
АО "Механобр - Техника" разработало и создало ряд технологий и машин, которые способны на месте разборки мусора перерабатывать все основное его компоненты с получением на выходе гранулированных и отсортированных пластмасс, целлюлозы, стеклянного порошка, сырой резины, компоста, металлического концентрата (из отходов электроники), отсортированного черного и цветного металла и щебня из отходов железобетона. Создан проект модульного мусороперерабатывающего завода без использования процесса сжигания, технологическая схема которого показана на рис. 6. Такой модульный завод может иметь производительность от 100 до 500 тыс. тонн в год.
Применяемые в модульном заводе технологические линии и оборудование освоены промышленностью и поставляются за рубеж (США, Германия, Франция, Япония, Финляндия). Завод мощностью 100 тыс. тонн в год окупает себя за 23 месяца, а заводы большей мощностью - за 15 - 18 месяцев. Если учесть, что в развитых странах правительственные субсидии на переработку мусора составляют $ 80 - 100 за 1 т, то в России нет другого пути, как обеспечивать самоокупаемость процесса переработки мусора методами регенерации.
Вайсберг Л.А., Зарогатский Л.П., Степанян А.С.
АО «Механобр - Техника»
Журнал "Вторичные ресурсы" №5-6 2001 год